QC Testing: Your Complete Guide
Author: The MuukTest Team
Published: April 10, 2025
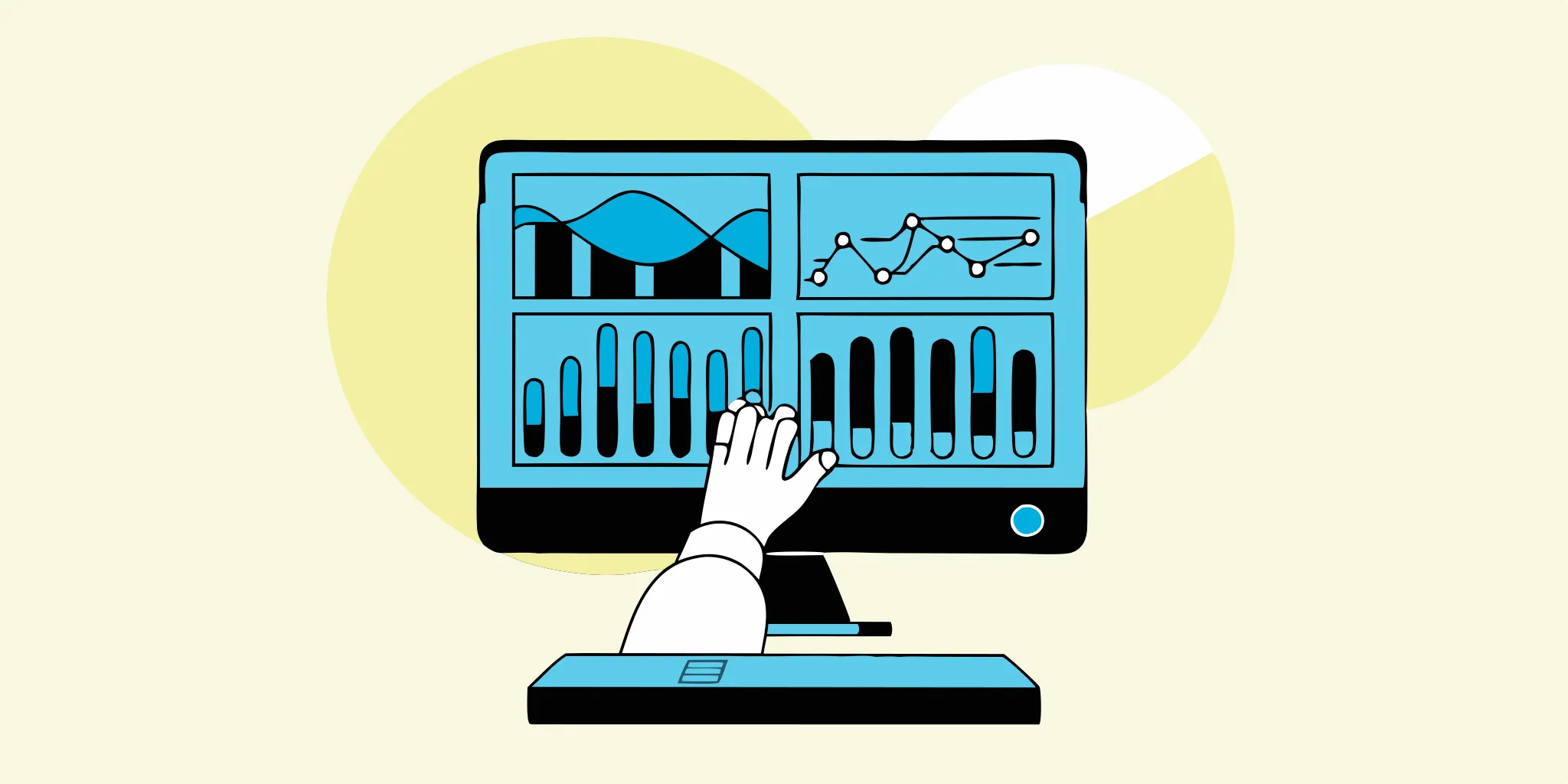
Table of Contents
Ever shipped a product with a hidden flaw? It's a sinking feeling, right? That's where quality control (QC) testing comes in. Think of it as your product's personal bodyguard, protecting it from bugs, inconsistencies, and anything that could disappoint your customers. From catching a misaligned seam on a designer dress to ensuring a software update doesn't introduce new glitches, a solid QC test process is the backbone of any successful business. In this guide, we'll break down everything you need to know about QC testing, from defining clear quality standards to leveraging the latest tools and technologies. Whether you're in manufacturing, software development, or any other industry, this guide will help you build a QC process that protects your brand and keeps your customers happy.
Key Takeaways
- QC testing is crucial for product excellence and customer satisfaction: It safeguards against defects, builds brand trust, and ultimately saves businesses money by catching issues early on. A strong QC process involves clear quality standards, robust testing methods, and a company-wide commitment to quality.
- QA and QC are distinct but complementary: QA establishes preventative processes, while QC focuses on identifying and rectifying defects in the finished product. Both are essential for a well-rounded quality management system.
- The QC landscape is constantly evolving: Trends like shift-left testing, cloud-based solutions, and AI-powered tools are reshaping quality control. Staying current with these advancements is key for any business looking to maintain high standards and a competitive edge.
What is Quality Control (QC) Testing?
Quality control (QC) testing is how companies ensure their products or services meet specific quality standards. Think of it as a systematic check-up at different production stages—from raw materials to finished goods—to catch and fix any issues. This rigorous process is essential for maintaining customer satisfaction, protecting brand reputation, and adhering to industry regulations. It's about making sure everything works as expected and lives up to the promised quality. For software, this could mean ensuring an app functions smoothly and is free of bugs. For a clothing manufacturer, it might involve checking seams and fabric quality.
Definition and Purpose
QC testing aims to identify defects early on, preventing faulty products from reaching customers. The earlier issues are identified, the less costly they are to fix. This proactive approach saves businesses money and protects their reputation. QC testing helps companies maintain consistent quality, meet customer expectations, and comply with industry standards. It's a critical part of any successful business, regardless of size or industry.
Key Components of QC Testing
Several methods and techniques help track and improve quality. These can range from simple visual inspections to sophisticated automated tests. Common QC methods include control charts, which visually track key metrics over time, and the 100% inspection method, where every single item is examined. The specific components of a QC process depend on the industry and the product being tested. A typical software QC process might involve stages like requirements analysis, test planning, test design, and test execution. Various techniques ensure the software is free from bugs and meets specified requirements. Regardless of the specific methods used, the goal remains the same: to identify and address quality issues before they impact the end-user.
QC Tests Across Industries
Quality control (QC) testing looks different across industries, each with unique requirements and priorities. Let's explore some examples:
Manufacturing: Dimensional Inspections
In manufacturing, QC often involves dimensional inspections. These inspections ensure products meet precise specifications for size, shape, and other physical attributes. Think about something like a car part—it needs to fit perfectly with other components, so precise measurements are critical. Testing might involve tools like calipers, micrometers, and even 3D scanners to catch deviations early in the production process.
Pharmaceuticals: Stability Testing
For pharmaceuticals, stability testing is paramount. Pharmaceutical companies need to guarantee their medications remain effective and safe throughout their shelf life. This means testing products under various conditions, like temperature and humidity fluctuations, to see how they hold up over time. This rigorous testing ensures medications don't degrade or become less potent before their expiration date.
Food Production: Microbiological Testing
Food production relies heavily on microbiological testing. This type of QC ensures food is safe for consumption by checking for harmful bacteria, viruses, and other pathogens. Regular testing helps companies maintain hygiene standards, verify ingredient quality, and prevent contaminated products from reaching consumers.
Software Development: Regression Testing
In the fast-paced world of software development, regression testing is essential. Every time a code change is implemented, regression testing ensures existing features still function correctly. It's like double-checking everything works as expected after making adjustments, preventing new bugs from impacting the user experience. At MuukTest, we specialize in helping software companies achieve comprehensive regression testing quickly and efficiently. You can learn more about our services on our website.
Environmental: Water Quality Testing
Environmental QC often involves water quality testing. This process assesses the safety and cleanliness of various water sources, from drinking water to wastewater. Testing for contaminants, pollutants, and other impurities helps protect both human health and the environment.
QC Testing vs. Quality Assurance: What's the Difference?
While both quality control (QC) and quality assurance (QA) are crucial for delivering high-quality products, they have distinct roles. Understanding these differences is key to building a robust quality management system.
Roles in Quality Management
Quality assurance focuses on preventing defects. It establishes processes and standards before development begins to minimize potential problems. Think of QA as the blueprint for quality. It's a preventative, managerial tool used throughout the entire project lifecycle. QA ensures the final product meets requirements by addressing potential issues early on. Quality control, on the other hand, focuses on identifying and fixing defects after the software is developed. It's about inspecting the finished product and making sure it adheres to the pre-defined standards set by the QA process. QC is a corrective tool, primarily used by the testing team to catch and fix flaws before the product reaches the customer.
When to Use QC and QA
QA activities span the entire software development lifecycle (SDLC). From requirements gathering to design, development, and testing, QA is involved at every stage to prevent defects. QC, however, comes into play primarily after the product is developed. It verifies the final product meets the standards defined by the QA process. Think of it this way: QA builds the foundation for quality, while QC inspects the structure built upon that foundation. QA is about long-term process improvement, while QC offers immediate feedback on the product's quality. This makes QC essential for catching any remaining defects before release.
Why QC Testing Matters for Businesses and Consumers
Quality control testing is critical for any business that creates products. It's more than just a step in production—it directly impacts your bottom line, brand reputation, and, most importantly, the safety and satisfaction of your customers. Let's explore why.
Ensure Product Safety and Compliance
Quality control processes act as a safety net, catching potential hazards before they reach the public. Rigorous testing helps identify defects, malfunctions, and other issues that could compromise product safety. This is particularly important in industries with stringent regulations, such as pharmaceuticals and food production. By adhering to quality control standards, businesses demonstrate their commitment to consumer safety and reduce the risk of costly recalls or legal action. Meeting these standards also builds trust and credibility with regulatory bodies, leading to smoother operations and market access.
Maintain Customer Satisfaction and Brand Reputation
In a competitive landscape, customer satisfaction is paramount. Delivering high-quality, reliable products is essential for building a loyal customer base and a positive brand reputation. Effective QC testing ensures products meet customer expectations and perform as intended. When customers receive products free from defects that function flawlessly, they are more likely to become repeat buyers and recommend your brand. Conversely, one negative experience with a faulty product can quickly damage your brand's image and erode customer trust. Investing in robust QC testing is investing in long-term customer relationships and sustainable business growth. Learn how MuukTest helps businesses maintain high standards with our customer success stories.
Save Costs and Increase Efficiency
While QC testing may seem like an added expense, it can save businesses significant money in the long run. Identifying and addressing defects early in the production process is far more cost-effective than dealing with product recalls, warranty claims, and reputational damage later. Early detection of problems allows for quicker corrective actions, minimizing wasted resources and production downtime. Streamlined QC processes also contribute to increased efficiency by optimizing production workflows and reducing errors. By preventing problems before they escalate, businesses can improve overall productivity and profitability. The cost of fixing bugs increases exponentially throughout the software development lifecycle, making early and thorough QC testing a financially sound strategy. MuukTest's services can help your business achieve comprehensive test coverage efficiently and cost-effectively. Get started with our quickstart guide or explore our pricing plans.
Implement an Effective QC Testing Process
Want to create a QC process that actually works? Here’s how to build a system that catches errors before they become problems:
Define Clear Quality Standards
First, define what “quality” means for your product or service. This might involve adopting a recognized quality management system like ISO 9001 to ensure consistent standards. Document these standards clearly so everyone on your team understands the benchmarks. Think of it as creating a shared understanding of what you’re all working toward.
Develop Robust Testing Protocols
Next, figure out how you’ll test for those standards. This means outlining the specific procedures for each test, including the steps, tools, and acceptance criteria. Consider the potential challenges you might face, such as balancing speed and quality or managing complex test environments, and build solutions into your protocols from the start. For software testing, MuukTest offers helpful insights into common QC challenges and how to address them.
Create Detailed Test Plans
Once you’ve set your standards and testing protocols, create detailed test plans for each product or feature. These plans should outline the specific tests you’ll run (like unit, integration, system, and acceptance testing), the testing environment, the tools you’ll use, and the metrics you’ll track. This guide provides a comprehensive overview of different testing types and strategies. Remember, a well-defined plan keeps everyone on the same page and ensures thorough testing.
Foster a Culture of Quality
Finally, remember that QC isn’t just a process; it’s a mindset. Cultivate a culture where quality is everyone’s responsibility. This starts with leadership clearly articulating the company’s values and demonstrating a commitment to quality in their own decisions. Articles on leadership practices offer further insights into building a strong organizational culture. When quality is embedded in your company culture, everyone becomes invested in producing the best possible product or service.
Tools and Technologies in Modern QC Testing
Quality control testing relies on a range of tools and technologies, from traditional equipment to cutting-edge software. Understanding these tools is key for any QA professional. Let's explore some essential categories.
Traditional QC Testing Equipment
Traditional QC testing often involves physical tools and equipment. Think of things like calipers and micrometers for precise measurements in manufacturing, or specialized equipment for material testing. These tools are essential for checking physical properties, dimensions, and other tangible aspects of a product. For example, a food production facility might use thermometers to ensure safe food storage temperatures, while a textile company might use light boxes to evaluate fabric color consistency. These tools provide a hands-on approach to quality verification.
Advanced Technologies and Automation
As technology evolves, so do the tools used in QC testing. Automated testing systems are becoming increasingly common, allowing for faster and more efficient testing processes. These systems can range from simple scripts that automate repetitive tasks to complex software platforms that manage entire testing workflows. MuukTest offers automation to streamline software testing, integrating directly into your CI/CD process and running tests quickly. This shift toward automation not only speeds up testing but also reduces the risk of human error, leading to more reliable results. Advanced testing tools that support diverse environments and technologies can also simplify the process.
AI and Machine Learning in QC
Artificial intelligence (AI) and machine learning (ML) are transforming the landscape of QC testing. These technologies can analyze vast amounts of data to identify patterns and anomalies that might be missed by traditional methods. AI-powered tools can predict potential quality issues before they occur, allowing for proactive interventions. MuukTest's AI agent automates much of the software QA testing process and simplifies test creation. By leveraging AI and ML, companies can achieve more comprehensive and efficient quality control, ultimately leading to higher quality products and greater customer satisfaction.
Overcome Common QC Testing Challenges
Implementing a robust quality control (QC) testing process is crucial for any business that wants to deliver high-quality products and services. However, teams often encounter several common challenges that can hinder their QC efforts. Let's explore some of these obstacles and discuss practical strategies to address them.
Resource Allocation and Cultural Resistance
One of the biggest hurdles in QC testing is securing adequate resources. This includes not only budget for testing tools and personnel but also dedicated time for testing activities. It's essential to demonstrate the return on investment of QC to stakeholders. Highlight how effective QC processes can reduce costs associated with defects, product recalls, and customer dissatisfaction. Beyond resources, cultural resistance to change can also impede progress. Some teams may view QC as an added burden rather than an integral part of the development lifecycle. To address this, foster a culture of quality by emphasizing the importance of QC in achieving business goals and recognizing individual contributions to quality improvement.
Maintain Consistency Across Teams
Maintaining consistency in QC practices across different teams and departments can be a significant challenge, especially in larger organizations. Variations in testing procedures, tools, and reporting can lead to inconsistencies in quality levels. Establish standardized testing protocols and documentation that all teams can follow. This ensures everyone is on the same page and helps maintain uniform quality standards across the organization. Regular communication and collaboration between teams are also essential for sharing best practices and addressing any discrepancies.
Integration Complexity
Integrating QC processes with existing development workflows can be complex, particularly when dealing with legacy systems or multiple software platforms. Seamless integration is key to ensuring that QC is embedded throughout the development lifecycle. Explore tools and technologies that facilitate integration with your current systems. For a streamlined approach to software QC, consider MuukTest, which offers solutions designed to integrate seamlessly with development workflows. Consider implementing a phased approach to integration, starting with pilot projects to test and refine the process before full-scale implementation.
Strategies for Continuous Improvement
QC testing shouldn't be a static process. Continuous improvement is essential for staying ahead of evolving quality standards and customer expectations. Regularly review your QC processes, gather feedback from teams, and analyze testing data to identify areas for optimization. Encourage a culture of continuous learning and improvement by providing training opportunities for your QC team to stay updated on the latest testing methodologies and technologies. By embracing these strategies, you can overcome common QC testing challenges and build a robust quality management system that drives business success.
Best Practices for QC Testing Success
Want to create a truly effective QC process? Here’s how to get the most from your efforts:
Integrate QC Early in Development
Think of quality control like building a house. It’s much easier to adjust the foundation in the early stages of construction than it is to fix cracks in the walls later on. The same principle applies to product development. Integrating QC from the beginning—sometimes called “shift left testing”—helps catch defects early, saving you time and resources. Proper planning, employee buy-in, and the right tools are essential for overcoming implementation challenges and fostering a culture of improvement.
Leverage Automated Testing Tools
We all know time is money. Automating your tests frees up your team to focus on more complex issues. Tools like MuukTest’s Amikoo can analyze your application, design tests, and automate entire test cases, significantly speeding up your QC process. This also ensures consistent testing and reduces the risk of human error. For more information on MuukTest's services, check out their test automation services page.
Establish Clear Metrics
How do you know if your QC process is working? You need to define what success looks like. Establishing clear, measurable metrics allows you to track progress, identify areas for improvement, and demonstrate the value of your QC efforts. Think about metrics like defect rate, test coverage, and time to resolution. Robust testing processes and a quality-driven culture are key to effective QA. For a quick start, see MuukTest's QuickStart guide.
Foster Collaboration Between Teams
QC isn’t a solo act. It requires clear communication and collaboration between developers, testers, and other stakeholders. Open communication channels and shared goals help ensure everyone is on the same page and working towards a common objective. While vital, this collaboration can be challenging when balancing testing with bug fixing. Learn more about how MuukTest works with its customers.
Regularly Review and Adapt Processes
The world of quality control is constantly evolving. Regularly reviewing and adapting your processes is crucial to staying ahead of the curve. This includes evaluating the effectiveness of your tools, refining your metrics, and incorporating feedback from your team. Addressing key challenges in QC and adapting processes is crucial for long-term success. A flexible QC process is a successful one. Check out MuukTest's pricing to see how they can help.
The Future of QC Testing: Trends and Innovations
The world of quality control (QC) testing is constantly evolving. Staying ahead of the curve means understanding and adapting to emerging trends and innovations. Let's explore some key areas shaping the future of QC.
Shift-Left Testing and Continuous Testing
We're seeing a significant shift toward integrating testing earlier in the software development lifecycle. This "shift-left" approach emphasizes testing from the very beginning, rather than waiting until the end of the development process. This helps identify and address defects sooner, saving time and resources. Shift-left testing naturally aligns with the principles of continuous testing, where testing is an ongoing process integrated throughout development. This ensures quality is baked in at every stage, leading to more robust and reliable software. This approach also supports faster release cycles and quicker feedback loops, crucial for staying competitive.
Cloud-Based QC Solutions
Cloud-based QC solutions are transforming how testing is conducted. These solutions offer the scalability and flexibility to adapt to changing project needs. Cloud platforms provide a cost-effective way to access powerful testing environments without the overhead of managing physical infrastructure. Services like MuukTest enable seamless integration into CI/CD pipelines, streamlining the testing process and accelerating delivery. This allows teams to focus on building high-quality software.
Prepare for Evolving Quality Control Standards
Quality control standards are not static. They're constantly evolving to meet new challenges and incorporate advancements in technology. Organizations need to stay informed about these changes and adapt their QC processes accordingly. The 2023 Quality Engineering Trends Report from Deloitte highlights key trends shaping the future of testing, emphasizing the need for adaptability and innovation in quality assurance practices. Staying current with industry standards and best practices is essential for maintaining a competitive edge and delivering products that meet customer expectations.
Frequently Asked Questions
What's the main difference between QA and QC?
Quality assurance (QA) focuses on preventing defects by establishing processes and standards before development begins. Quality control (QC), on the other hand, focuses on identifying and fixing defects after the product is developed. Think of QA as setting the stage for quality, while QC ensures the performance meets the standards set.
How can I implement an effective QC process in my company?
Start by defining clear quality standards and developing robust testing protocols. Create detailed test plans for each product or feature, outlining the specific tests, environment, tools, and metrics. Most importantly, foster a culture of quality where everyone is responsible for delivering high-quality work.
What are some common challenges in QC testing, and how can I overcome them?
Common challenges include limited resources, resistance to change within the company culture, maintaining consistency across teams, and the complexity of integrating QC into existing workflows. You can address these by demonstrating the value of QC, establishing clear standards and communication channels, and exploring tools that streamline integration.
What are some of the latest trends in QC testing?
Key trends include "shift-left" testing (integrating testing earlier in the development lifecycle), continuous testing, the rise of cloud-based QC solutions, and the increasing use of AI and machine learning in automating and enhancing QC processes. Staying informed about these trends is crucial for maintaining a competitive edge.
Why is QC testing important for my business?
QC testing is crucial for ensuring product safety, maintaining customer satisfaction, protecting your brand's reputation, and ultimately saving your business time and money. By catching defects early, you avoid costly recalls, improve efficiency, and build stronger customer relationships.
Related Posts:
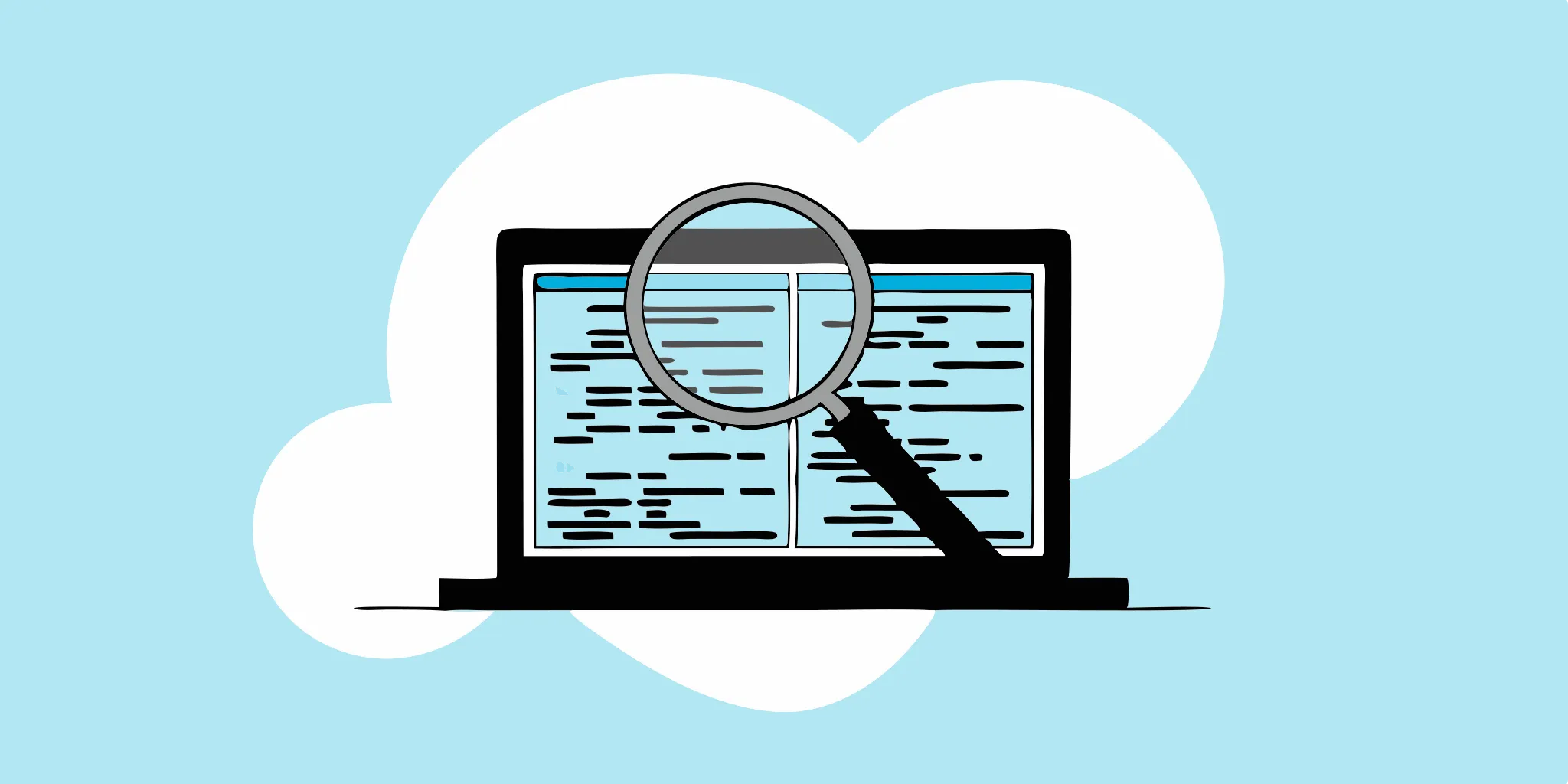
Quality Control Testing: A Practical Guide
Learn effective quality control testing strategies to ensure reliable software. Explore methodologies, tools, and best practices for comprehensive testing.
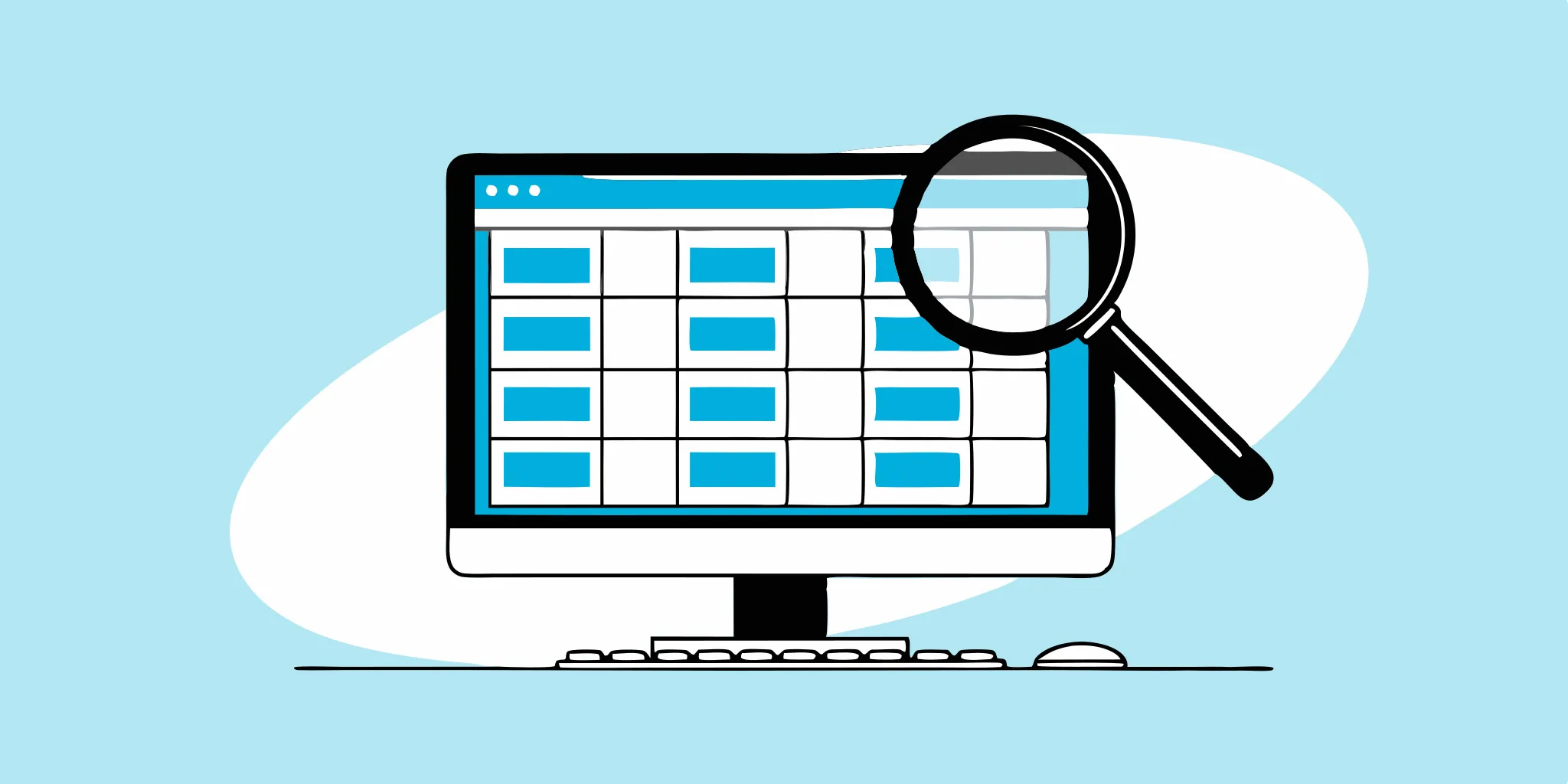
Software Quality Control: A Practical Guide
Releasing software riddled with bugs is a nightmare scenario for any development team. That's where software quality control (SQC) comes in. SQC is your first line of defense against software...
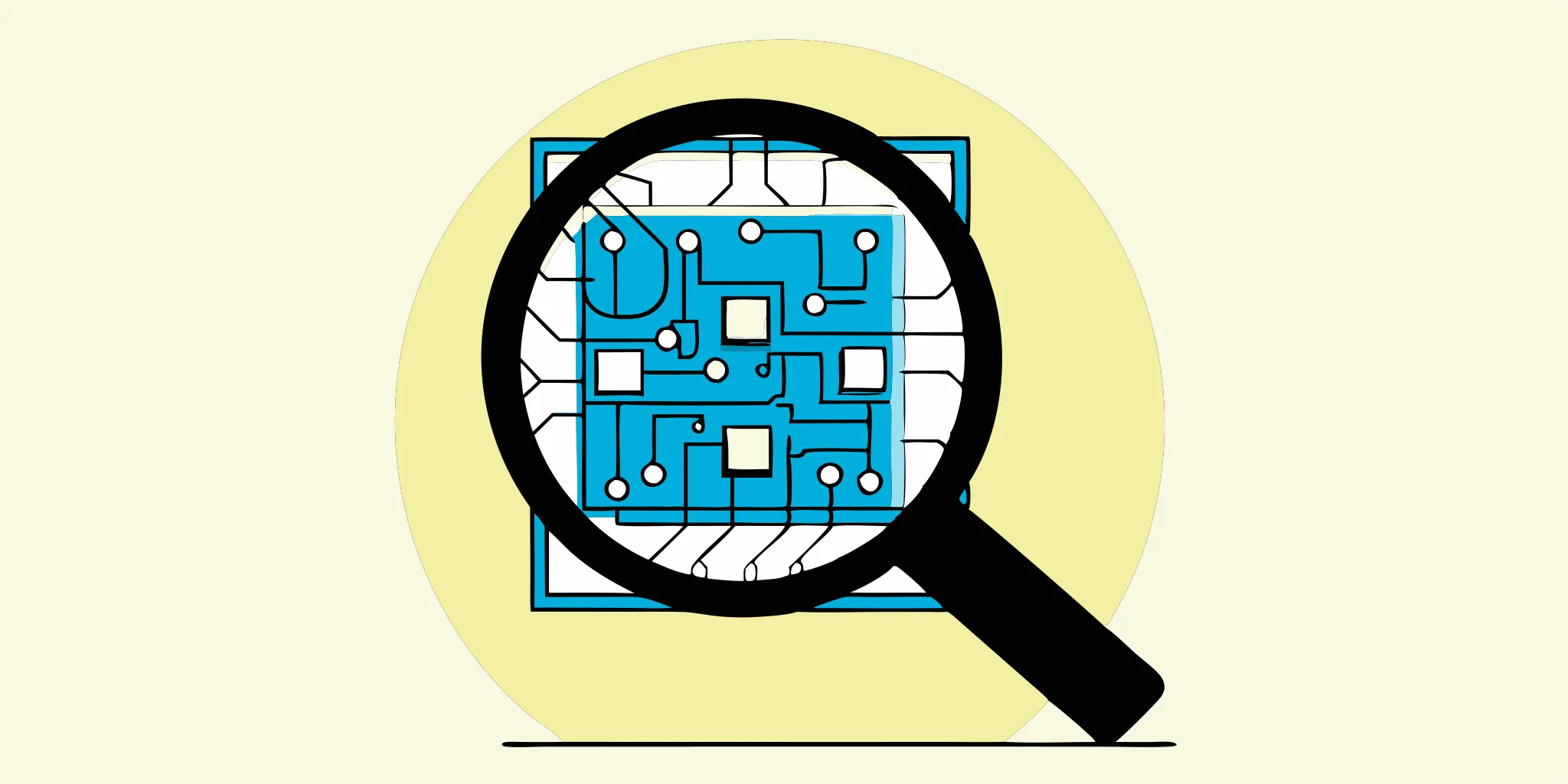
Quality Testing: Your Complete Guide
Master quality testing with this comprehensive guide, covering essential methods, best practices, and strategies to ensure your product meets high standards.